Top Pressure Die Casting Suppliers for Your Metal Fabrication Needs
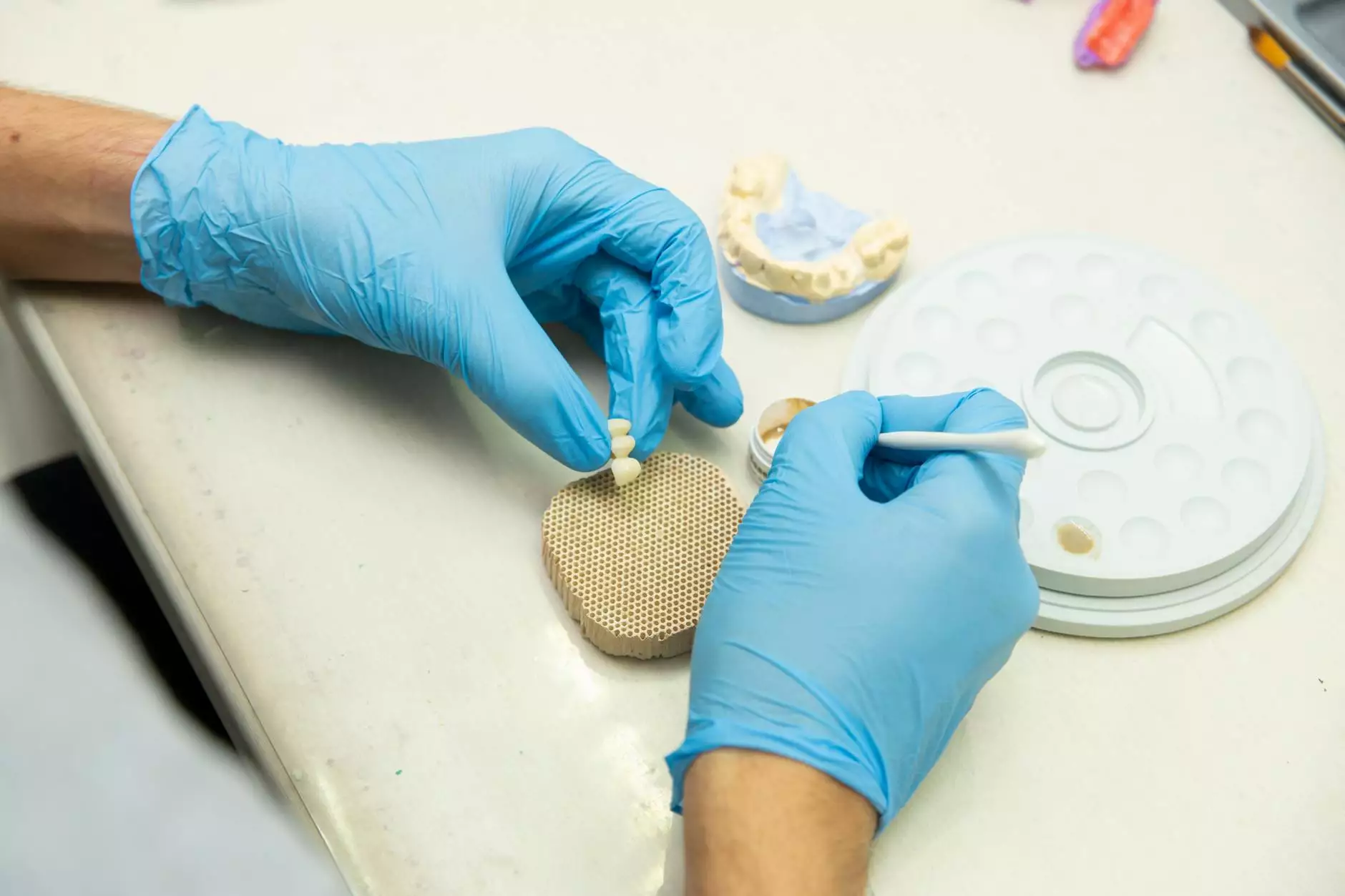
The process of pressure die casting is a pivotal method in metal fabrication, renowned for its ability to produce components with exceptional precision and surface finish. If you're in the market for high-quality castings, recognizing the best pressure die casting suppliers is crucial. This comprehensive article will delve into what defines the top suppliers in this niche, their benefits, and how to select the right partner for your business. Whether you're in automotive, aerospace, or any industrial application, understanding this process is essential.
Understanding Pressure Die Casting
Pressure die casting is a manufacturing process where molten metal is injected into a mold under high pressure. This technique offers numerous advantages, including:
- High Precision: Molds can produce components with tight tolerances.
- Excellent Surface Finish: The casting process results in smooth surface finishes that often require little to no machining.
- Complex Geometries: Capable of creating intricate shapes that are difficult to achieve with other manufacturing methods.
- Rapid Production: Ideal for high-volume production runs thanks to short cycle times.
The Importance of Choosing the Right Supplier
Selecting the right pressure die casting supplier can significantly impact your production efficiency, costs, and end product quality. Here are key factors to consider:
1. Experience and Expertise
Years in the industry often translate to expertise. A seasoned provider will have upgraded their techniques and technologies, ensuring superior quality. Ask about their past projects, sectors served, and specific casting challenges they have overcome.
2. Technology and Equipment
The best pressure die casting suppliers invest in state-of-the-art technology and machinery. This includes computer numerical control (CNC) machines, automated processes, and high-quality molds. Advanced technology can enhance precision and reduce waste.
3. Material Selection
Quality suppliers offer a diverse range of materials, including:
- Aluminum: Light, corrosion-resistant, great for automotive and aerospace applications.
- Zinc: Ideal for intricate shapes and provides excellent strength.
- Magnesium: Known for its low weight and high strength.
Understanding the material options available can significantly affect the performance of your final product.
Top Benefits of Using Reputable Suppliers
Choosing reliable pressure die casting suppliers leads to numerous benefits that contribute to the success of your project:
1. Consistency and Quality Assurance
Leading suppliers prioritize quality control throughout the casting process. They implement ISO standards or other relevant certifications to ensure that every batch meets the specified requirements.
2. Cost Efficiency
Experienced suppliers can help streamline the production process, reducing waste and optimizing material usage, which translates into cost savings. Additionally, they can provide insight on batch sizes that lead to cost-effective production runs.
3. Short Lead Times
Suppliers with advanced capabilities often can reduce lead times significantly, allowing you to bring your product to market faster. This is particularly vital in manufacturing environments where timing is crucial.
How to Evaluate Pressure Die Casting Suppliers
Here’s a structured approach to evaluate potential pressure die casting suppliers:
- Request Quotes: Gather detailed quotes from multiple suppliers to compare costs and services offered.
- Visit Their Facility: A personal visit allows you to assess their operations and capabilities firsthand.
- Ask for References: Inquire about past clients and projects to gauge their reliability.
- Review Portfolios: Look at the complexity and quality of past projects to ascertain their capabilities.
Industry Applications of Pressure Die Casting
Pressure die casting is fundamental across various industries. Here are some of the most significant applications:
1. Automotive Industry
In the automotive sector, components like engine blocks, transmission housings, and other structural elements benefit from the precision and strength provided by die casting methods.
2. Aerospace Applications
Lightweight and high-strength components are essential for aerospace applications. Die casting allows manufacturers to produce parts that meet stringent regulatory standards and performance expectations.
3. Consumer Electronics
Many consumer electronics feature die-cast aluminum casings. This technique enhances durability while maintaining a lightweight profile, ideal for handheld devices.
Conclusion: Partnering with the Best Suppliers
Finding the right pressure die casting suppliers can drastically affect the quality, efficiency, and cost of your production process. It's crucial to conduct thorough research, evaluate potential partners, and consider their industry expertise, technological capabilities, and material offerings.
By aligning with a reputable supplier like Deep Mould, you can ensure that your project meets all specifications and maintains high standards. With their extensive experience in metal fabrication and commitment to quality, they stand out in the competitive landscape of pressure die casting. Secure your business's success today by choosing wisely and leveraging the benefits that the best suppliers can offer.